National contact
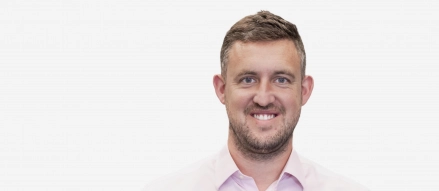
In recent years they had been making an operating loss and suspected this was caused by the inefficient use of materials and weakened controls around metals leaving the premises.
There were questions over whether the metal runoff in the casting process was being reused effectively, or whether it was sold for scrap unnecessarily. Losses may have been further exacerbated by the process for selling surplus scrap metal, which did not provide strong confidence that everything that was sold was then invoiced.
Given the upcoming annual stock take, our client was keen to take this opportunity to evaluate its processes around the purchase, use and sale of metals. We were engaged to carry out this review, report on the results, and provide suggestions for improvement.
In order to obtain an understanding of the current processes on the use of metals, we led interviews and walkthroughs with key staff. This allowed us to map the processes under review from start to finish, which in turn made it easier to identify areas of weakened control and manual intervention. Each process was also observed in practice to validate the accuracy of our understanding and confirm the presence of identified issues.
We also built a tracking model that accurately predicted closing stock based on the opening values, purchase data and usage data. The model further calculated the monthly cost of materials used. We then used the model's outputs alongside the findings of our review to help the client understand where there may be discrepancies between their accounts and actual production costs. Notably, a large quantity of metals purchased was never used, resulting in unnecessarily high material costs.
The outcome of the review was the creation of a metals stock tracker, as well as the issue of prioritised recommendations for improving efficiency and reducing costs, including
Since the review concluded in August 2020, the client has put in place several of our recommendations, resulting in £250k in material cost savings this quarter. This equates to a change in gross profit margin from 15.8% to 22.5.
If you would like to understand how our teams can support your business, please do not hesitate to get in touch.
This website uses cookies.
Some of these cookies are necessary, while others help us analyse our traffic, serve advertising and deliver customised experiences for you.
For more information on the cookies we use, please refer to our Privacy Policy.
This website cannot function properly without these cookies.
Analytical cookies help us enhance our website by collecting information on its usage.
We use marketing cookies to increase the relevancy of our advertising campaigns.